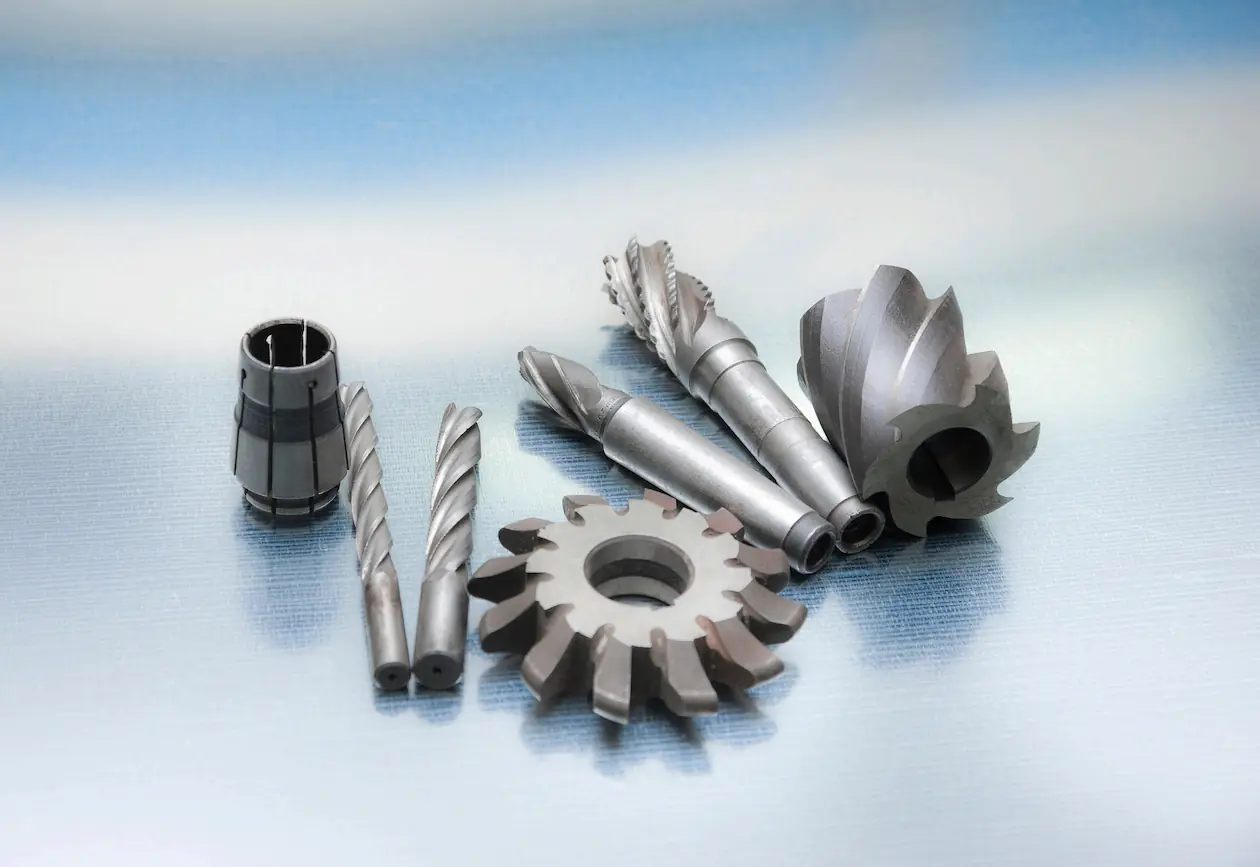
Aluminum machining refers to the precision process of cutting, shaping, and finishing aluminum materials using various techniques such as CNC milling, turning, drilling, and more. Aluminum has the properties of lightweight, corrosion resistant and durable and successfully used in many industries such as aerospace, automobile, electronics, and consumer goods manufacturing. Aluminum machining enables the production of complex parts with high accuracy and efficiency, making it a preferred choice for custom parts, prototypes, and high-volume production runs.
What is Aluminum Machining?
Aluminum machining refers to the precision process of cutting, shaping, and finishing aluminum materials using various techniques such as CNC milling, turning, drilling, and more. Aluminum has the properties of lightweight, corrosion resistant and durable and successfully used in many industries such as aerospace, automobile, electronics, and consumer goods manufacturing. Aluminum machining enables the production of complex parts with high accuracy and efficiency, making it a preferred choice for custom parts, prototypes, and high-volume production runs.
How Aluminum Machining Works: Key Processes
The process of aluminum machining consists of several precise steps to create parts that meet exact specifications:
Material Selection and Preparation: The key to selecting the right aluminum alloy (e.g. 6061 or 7075) for the ultimate alloy in the final product. The performance of the machined part is influenced by the machinable characteristics of each alloy: strength, hardness and machinability.
CNC Milling and Turning: CNC milling and turning are key methods in aluminum machining. Second, CNC milling is used to cut and shape aluminum parts to perform intricate designs using rotating tools. In contrast, CNC turning, shapes and other symmetrical features in the aluminum workpiece by rotating the workpiece and cutting tools that remove material.
Drilling, Tapping, and Threading: The use of these processes is often to reduce aluminum parts and to add holes, threads and other details. The part was prepared for assembly or function by high precision drills and taps, and the threads are durable and positioned precisely.
Finishing and Surface Treatment: Aluminum machining frequently includes surface finishing and treatments, such as anodizing, powder coating, or polishing, to enhance appearance, corrosion resistance, and wear protection. Powder coating, for instance, can provide a desired color; anodizing can add a protective oxide layer; and so on.
Quality Inspection: After machining, all the parts are then subjected to an exhaustive set of examined to determine dimensional accuracy, surface finish, and overall strength. This step is done as a way to confirm the part meets the required specifications before we send it to the client.
Our Advantages in Aluminum Machining
DUNTEK‘s aluminum machining services offer several distinct advantages:
Precision and Efficiency: With state of the art CNC machines and a very skilled team, we are capable of producing parts with very precise tolerances, regardless of the complexity. We machine efficiently to meet tight deadlines and large orders with no loss to quality.
Material Expertise and Versatility: Different combinations for each aluminum alloy, as we tailor each choice to the necessary requirements of the client on his specific project. This material versatility allows us to serve the entire range of industry and application, from lightweight aerospace components to rugged automotive parts.
Consistent Quality Control: Quality is very important at DUNTEK. With our strict inspection protocols and state-of-the-art measuring tools, we are able to always deliver parts that meet the highest quality standards. The various parts are checked for dimension accuracy, surface finish and quality of the whole.
Eco-Conscious Practices: DUNTEK follows eco-friendly machining practice and recyclable aluminum, so we minimize the waste, use limited material and reduce the environment footprint.
How We Meet Client Needs in Aluminum Machining
DUNTEK‘s aluminum machining services are designed with client satisfaction and adaptability in mind:
Custom Solutions Across Industries: We design and produce industry specific solutions across high performance automotive parts, precision medical equipment and complex aerospace components. When you know what each industry’s demand is, you see what it’s going to need on a custom machined part level.
Flexible Production Options: Whether clients require rapid prototyping for testing purposes or full-scale production, we offer flexible manufacturing services that can scale to meet varying production needs, from one-off parts to high-volume orders.
Fast Turnaround Times: Our streamlined aluminum machining process allows us to produce and deliver parts swiftly, helping clients maintain project timelines. There’s a lot to be said about a quick response time, especially for companies that have to get their prototypes and tests going as fast as possible.
Collaborative Design and Engineering Support: We work closely with clients to understand their project requirements and provide design-for-manufacturability advice. Finally, this collaboration guarantees parts are optimized for both performance and production efficiency.
Conclusion
DUNTEK‘s aluminum machining services offer a complete solution for clients seeking high-quality, custom aluminum parts. DUNTEK brings together precision machining, strict quality control, and the industry specific expertise to offer aluminum components that are reliable, cost-effective, and custom-made to suit each client. Require a quote or have a question? Get in touch with us now!