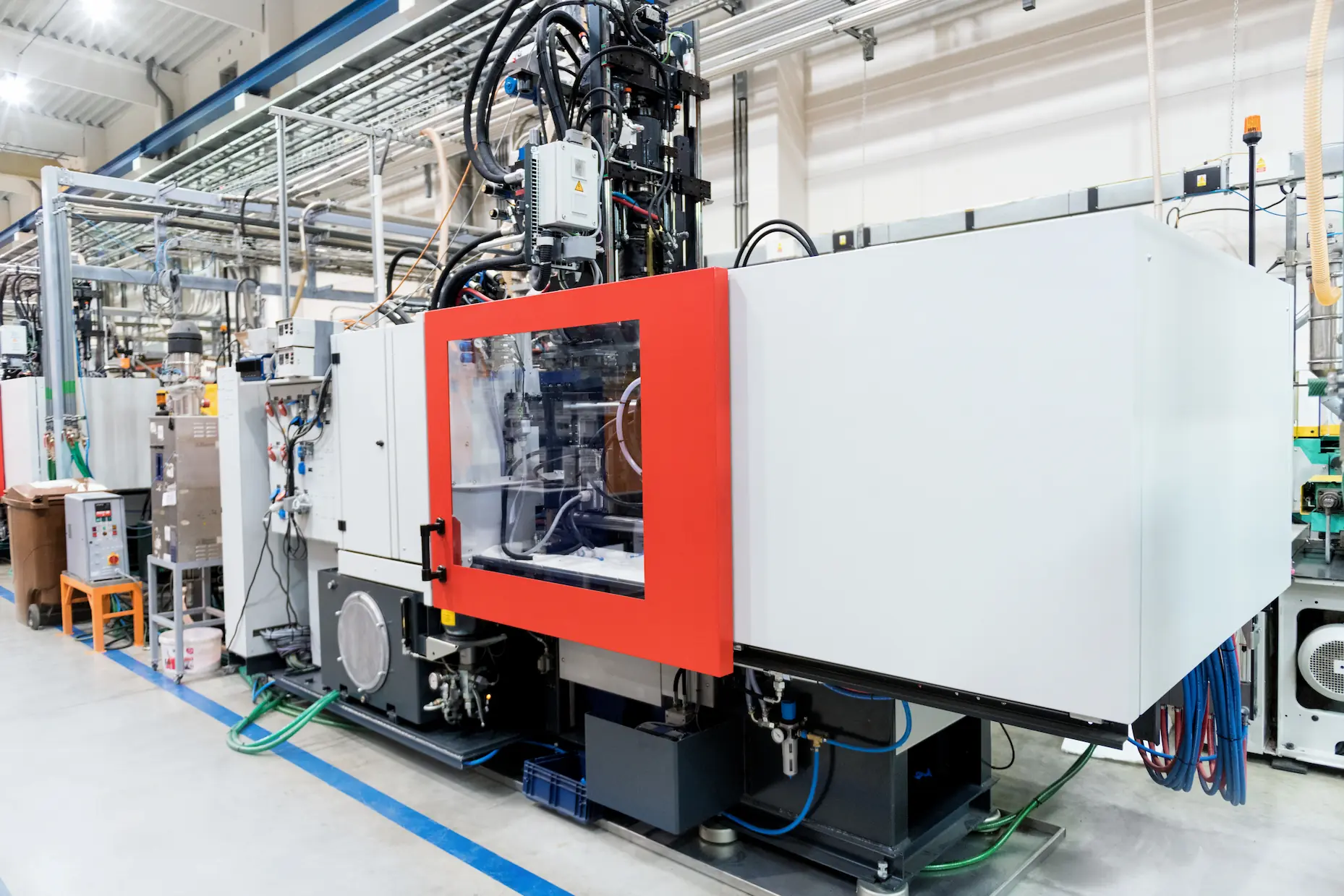
Aircraft and industrial gas turbines are critical components in aircraft and power generation and are relied upon for reliability and efficiency and for longevity. In the case of gas turbine machining in general, and in the machining of aircraft components; such as blades, rotors, and housings; high temperatures, high speeds, and intense pressure must be withstood. Motor machining precision affects turbine performance directly because even small faults can result in poorer efficiency, more maintenance costs, and in the most extreme circumstances, full shutdown of the systems.
Aircraft and Industrial Gas Turbine Machining: Understanding
Aircraft and industrial gas turbines are critical components in aircraft and power generation and are relied upon for reliability and efficiency and for longevity. In the case of gas turbine machining in general, and in the machining of aircraft components; such as blades, rotors, and housings; high temperatures, high speeds, and intense pressure must be withstood. Motor machining precision impacts turbine performance directly because even small faults can result in poorer efficiency, more maintenance costs, and in the most extreme circumstances, full shutdown of the systems.
High temperature resistant and corrosion resistant materials are selected for use in gas turbines. The materials commonly machined include titanium, Income, and other high performance alloys which are especially difficult to machine because of the hard structure, high thermal sensitivity, and lower desired stretch. It is essential to address these challenges using advanced machining techniques and tools to deliver parts with long periods and extreme conditions functionality.
How Can We Reach the Required Precision in Turbine Machining?
DUNTEK embarks on gas turbine machining via application of high precision CNC machining and predicated milling and grinding methods, aiming to cope with the intricate shapes and stringent requirements of turbine components. Our machining processes for gas turbines include:
Material Analysis and Preparation: We do a comprehensive material analysis before we can begin machining. This time we know the material’s properties like its hardness, temperature tolerance and machinability so we can tune cutting speed, tool path and coolant applications based on these. Our thermal stable fixtures minimize any part positioning shifts from the first cut to the last for precision.
High-Precision CNC Milling and Turning: We use multi axis CNC machining to machine the intricate shapes and tight tolerances demanded by turbine blades and rotors. Achieving the aerodynamics and precision that gas turbines require depends on this process. Because our CNC machines have very fine resolutions, we can still maintain accuracy with high complexity shapes. Such result causes turbine parts to yield maximum airflow and energy conversion efficiency (CNC machining service).
Grinding and Finishing: Surface finish is critical to gas turbine efficiency, especially for rotating components in which friction and drag must be minimized. This ultra smooth surface further improves the aerodynamic performance, and extends the service life of turbine components.
Quality Assurance: Quality checks are part and parcel of our process at every stage of production. All our factory parts are inspected by coordinate measuring machines (CMM) and laser scanners for dimensional accuracy, to the exact specs they need to be for aerospace or industrial purpose.
Our unique strengths in Gas Turbine Machining
DUNTEK’s approach to gas turbine machining offers distinct advantages that set us apart from the competition:
Advanced Tooling and Machining Technologies: Staying ahead of machining technology allows us to tackle the toughest of material and the tightest of tolerances. We have CNC machines that are optimized for high strength alloys that are as precise as possible without sacrificing speed or efficiency.
Highly Experienced Team: Both our engineering and machining teams have years of aerospace and industrial turbine manufacturing experience. With this depth of expertise, we can foresee and manage the murmurs of the gas turbine machining; optimizing the tool path and choosing the magic cutting tool, the smart coolant strategy.
Commitment to Sustainability: As manufacturers, however, we know that our processes can have an impact on the environment, and so we are very aware that we must minimize waste and energy consumption. All of our processes are aligned with industry best practices for sustainable manufacturing, enabling us to deliver precision parts with a reduced carbon footprint.
How We Meet the Needs of Our Clients
DUNTEK customizes our gas turbine machining solutions to meet each client’s unique specifications, while providing parts that are both functional and perform according to requirements. Here’s how we deliver on our commitment to quality and reliability:
Collaboration and Customization: For each project, we work closely with our clients to understand their specific requirements. The production of parts that meet the exact operational conditions for aircraft and industrial gas turbines can be optimized by tailoring our machining processes to each application.
Experience in Diverse Applications: We have a track record on projects for the aerospace and the industrial sector. And for example, a client needed us to machine high performance turbine blades. They also had to tolerate prolonged operation at elevated high temperatures without degrading. With our high temperature resistant machining techniques, we were able to deliver components that exceeded the client’s expectations in performance, and in the case of the durability of these components, reached well beyond their expectations.
Fast and Reliable Turnaround: For aerospace and industrial clients working on tight schedules, we ensure fast yet accurate machining, minimizing downtime without compromising quality. In high stakes manufacturing scenarios, where our leads may be as short as a day, we offer the time that you require while ensuring the highest quality standards.
Spare Parts Machining: External Insights and Trends
The aerospace, along with the industrial, sectors advance always with the invention of new materials and processes being implemented in order to satisfy increasing requirements for efficiency and sustainability. Gas turbine market is expected to grow remarkably, owing to the increasing demand for cleaner and efficient power sources (Allied Market Research). To respond to these trends, we’re continuing to refine our machining capabilities, staying ahead of industry standards and continually moving the envelope on what we can achieve.
Furthermore, past innovations in gas turbine production are further supported by the newer developments in the additive manufacturing field. When it comes to creating complex shapes, more and more we are turning to laser and electron beam melting to reduce the need for intensive machining processes, and improve component performance. Fast moving technologies like these beckon DUNTEK to explore how they can merge with the already set processes of our already established gas turbine manufacturing.
Work with DUNTEK in Precision and Reliability in Spare Parts Machining & Manufacturing for Aircraft & Gas Turbine
DUNTEK is trained with state-of-the-art equipment and team to meet the toughest gas turbine machining jobs on aerospace and industrial markets. We understand that precision and reliability are critical, and we’re dedicated to helping our clients achieve the highest standards in their products. Explore our services page to learn more, or contact us directly to see how we can support your manufacturing needs.